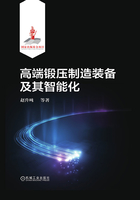
5.3 今后主要研究与开发的内容
5.3.1 铝合金在汽车中的应用
目前,铝合金件的冲铆工艺在国外已经广泛使用,各国使用情况见表5-6。
表5-6 各国使用情况

在欧洲、美国、日本等主要汽车生产企业中,轿车的覆盖件已部分或全部采用铝合金材料。如亨利福特Model-T型汽车、福特Prodigy、捷豹newXJ、法拉利360赛车、Daimler-Chrysler Prowler、VW3L、Lupo、奥迪A2、A8及本田混合动力轿车、NSX等车型的覆盖件全部为铝合金材料。福特Ranger、丰田Crown等采用铝合金覆盖件的部位主要集中在轿车的发动机盖板。其他车型,如雪铁龙C6、马自达RX-8、宝马5、7系列等,均在车顶、行李箱盖内外板、车门、发动机盖板和翼子板等部位也采用铝合金材料。
近几年,随着国外车型被不断引入中国,冲铆连接技术也被大量的带入中国汽车行业中,如富康、奥迪A6、帕萨特、宝来、广州本田等,尤其是上海大众2002年与世界同步推出的POLO轿车,首次在白车身上将TOX连接工艺大规模地带入中国。图5-21所示为POLO轿车的后行李箱,共79个TOX连接点。图5-22所示为无铆钉连接工艺在中国一汽大众汽车上的应用情况。图5-22a为行李箱内板,该部分的材料为5052铝合金,图5-22b为行李箱外板,使用了6×××系铝合金,即能够进行热处理强化、喷漆等处理的板料。图5-22c为翼子板,该部分材料为6061铝合金板料。图5-22d为前盖内板,使用5052铝合金板料。

图5-21 POLO轿车后行李箱盖

图5-22 应用无铆钉塑性成形连接的白车身零件
a)行李箱内板
b)行李箱外板 c)翼子板 d)前盖内板
5.3.2 国内冲铆技术与发达国家的差距
早在1897年,无铆连接技术就已经申请了专利,但是直到20世纪80年代末,无铆连接技术才被广泛应用于工业生产,主要原因是德国托克斯(TOX PRESSOTECHNIK)研究开发的专利技术,解决了传统连接方法难于实现的板材连接问题,实现了异种板材、镀层板材以及多层板材等板材的连接,极大地促进了轻质材料等在汽车工业中的应用。
理论上讲,金属板材具有一定的塑性变形能力,均可以采用冲铆连接。实际应用中常用的材料主要包括钢、铝(铝合金)以及其他带有涂层的有色金属。由于冲铆连接技术在经济、环保以及性能可靠性等各方面的突出优点,目前在世界范围内得到了广泛的认可和接受,并广泛应用于汽车工业和家电制造等行业。国外的一些知名汽车厂商,如奔驰、宝马、奥迪、大众、通用等,早已在车身制造业中广泛采用冲铆连接技术。在国内,该技术的应用才刚刚开始,一些汽车零配件厂也开始采用冲铆连接技术对汽车上的个别零部件进行连接生产。与发达国家存在很大的差距,主要表现在以下几个方面:
(1)前沿技术落后于发达国家 近年来我国的冲铆技术虽然取得了进展,但是仍落后于发达国家。
(2)模具设计理论及方法 由于板材成形过程中受到多种因素的影响,至今并没有一套公认的理论体系来描述无铆连接的成形机理,导致了无铆连接技术的发展至今仍处在科学试验阶段。国外在模拟技术、虚拟设计及软件开发等方面取得较多创新,基本上实现零试模或可大大减少试模次数,而国内尚未建立完整的、大型的数据库和专家库,软件开发刚刚起步,差距较大。
(3)在模具结构创新和精密现代化加工方面有较大差距 国外已开创出多种新的先进结构模具,加工精度达到了很高水平,能大批量生产,产品质量十分稳定,而我国在这方面还处于起步阶段。
(4)自动化程度低 目前,国内的冲铆设备主要包括手钳式和台式,与发达国家相比,其可靠性、运行平稳程度、可操控性等方面仍然存在差距。