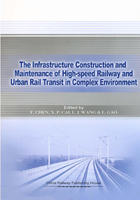
CONTRASTIVE ANALYSIS OF CHARACTERISTICS OF WHEEL/RAIL ROLLING CONTACT UNDER COMBINATION OF MULTI-BODY DYNAMICS SIMULATION WITH FINITE ELEMENT
Hui ZHANG,Xiangguo LI
Department of Transportation Engineering of College,Shijiazhuang Railway University,Shijiazhuang 050043
Abstract:Due to the development of overloaded railway and the high-speed rail,the problem of characteristics of wheel/rail rolling contact is researched by domestic and foreign scholars.This article first introduces the theory of wheel/rail rolling contact based on the Hertz theory.Then through the combination of UM multi-body dynamics simulation software with the finite element software ABAQUS,characteristics of wheel/rail rolling contact are analyzed contrastingly from different wheel on the transverse quantity and different friction coefficient.Wheel/rail damage to overloaded railway mainly includes the wheel/rail contact fatigue and wear,the driving stability is also directly influenced by wheel/rail wear on high speed railway,and the research on rolling contact fatigue of wheel/rail and wheel/rail wear problems is based on data such as elastic-plastic stress and strain appear in the course of wheel/rail rolling contact,so the research on the characteristic of wheel/rail rolling contact has a certain significance.The results show that:the results obtained by finite element method based on the theory of elastic-plastic is more visualized and closer to real;The transverse quantity mainly affects the normal characteristics of wheel-rail rolling contact;The maximum Mises stress and maximum normal contact stress appear in the working condition without transverse quantity;Attack Angle and friction coefficient mainly affects the tangential characteristics.
Keywords:characteristics of wheel/rail rolling contact,multi-body dynamics simulation,finite element,transverse quantity,Attack Angle,tangential characteristics
Email:zhanghui5258@qq.com
1 Wheel/Rail Rolling Contact Theory Based on Hertz Theory
Hertz used elastic mechanics theory to research the problem of contact of two elastomers,and put forward the Hertz elastic contact theory[1].
Hertz also expounded the condition of Formula(1)the normal displacement on the surface of the object must satisfy.

In the formula,δ=δ1+δ2is the moving displacements of the big internal distance of two objects;uz1,uz2are the normal displacement of the surface of two objects;Ax2+By2is the initial clearance of contact.
The initial clearance constants A and B of the contact surface function of wheel/rail can be determined by the following equation:


In the Formula(2)and Formula(3),is the radius of the round circle,
is the radius of the shape of cross sectional on tread,
is the radius of rail longitudinal curvature,
is the radius of shape of the cross section on rail[2].
2 Simulation and Calculation by Multi-body Dynamics Software UM
This article uses the whole model of the vehicle[3].According to the different methods of suspension,the vehicles are roughly divided into three types:one is the central suspension system,a truck axle suspension model and secondary suspension model.This paper uses the CRH2 as the prototype[4];UM simulation analysis software is used to establish the vehicle model.Partial parameters of the vehicle model are shown in Table 1.
Table 1 Parameters of vehicle model

Simulation of circuit parameter is as follows:500 m straight line,rail is 60 kg/m China standard cross section of new rail.Vehicle moves at a constant speed of 200 km/h on a straight line until the end of 5000 m.This paper uses irregularity spectrum of high speed railway track without slag released in 2015 by national railway administration in our country for motivation[5].
When train runs to 200 meters,results of the simulation are shown in Table 2.
Table 2 Data of simulation


Figure 1 Wheel/rail contact spot
3 Analysis of Wheel/Rail Rolling Contact Based on ABAQUS Finite Element
3.1 ABAQUS finite element model
The related parameters of wheel/rail contact finite element model as shown in Table 3.
Table 3 Wheel/rail contact finite element model parameters

In order to coordinate calculation precision and calculation efficiency,the grid on the head part of rail has been elaborated[6].Finally a model of the wheel with 37118 nodes is formed,24844 units and a model of rail with 8064 nodes,5832 units is formed.
This paper defines the coulomb friction model as the tangential relationship,defines“hard” contact as a normal relationship and defines the round surface of wheel as the principal surface,the surface of the rail head as the subordinate surface.About the contact,“small slip” is defined as the type of wheel/rail contact and the admissible error is set at 0.006to meet the elastic deformation in wheel/rail rolling contact which may cause small sliding on contact surface.

Figure 2 Assembly of wheel and rail

Figure 3 Detail of wheel/rail contact
3.2 Results of ABAQUS finite element method under the same working condition with UM simulation
Table 4 Results of ABAQUS finite element method

Compare the results of Table 1 with the results of Table 2,we can get to know that the results obtained by finite element method and the results obtained by multi-body dynamics simulation is different,but the difference is not big.They are all valid.Multi-body dynamics method is based on the theory of elasticity,while the finite element method is based on the theory of elastic-plastic.In fact,the material of wheel and rail are elastic plastic[7].So the results obtained by finite element method is closer to real.And the analysis by ABAQUS finite element can provide a three-dimensional display.
3.3 Influence of transverse quantity
Transverse quantity refers to the distance of the vertical centerline orbit round to the centerline.In this paper,the wheel/rail force is 13.920 kN,wheel angular velocity is 129.2 rad/s,and characteristics of wheel/rail contact with different transverse quantity were analyzed.At the moment,friction coefficient is 0.2,Angle of attack is 0 mard,horizontal shift values were taken respectively as 0,1 mm,3 mm,5 mm.Shape of contact spot ,area of contact spot,the maximum Mises stress and maximum normal contact stress are shown in Table 5.
By the Table 4 we can conclude that the characteristics of wheel/rail rolling contact and the transverse quantity have an affinity,as the transverse quantity increases gradually,the contact position changes,the area of the contact spot gradually increases;The maximum Mises stress on the contact area decreases on the overall trend with the increase of transverse quantity;The maximum normal contact stress on the contact area decreases on the overall trend with the increase of transverse quantity;Mises stress,the normal contact stress,the transverse shear stress and the longitudinal shear stress have the maximum value in the absence of transverse quantity.
Table 5 Results of ABAQUS with different transverse quantity

What can be seen from the Figure 4 and Figure 5 is that the maximum Mises stress appears on the rail contact surface;with the increase of wheel/rail transverse quantity,the maximum Mises reduces,the distribution area of Mises stress also tends to be reduced.It’s not hard to find that when wheel/rail lateral movement occurs,the position and size of the wheel/rail contact spot,the normal stress value and tangential stress value of the stress characteristics of wheel/rail rolling contact will change.
3.4 Influence of friction coefficient
This section does not consider transverse quantity and Attack Angle.The wheel/rail force is 13.920 kN,wheel angular velocity is 129.2 rad/s,characteristics of wheel/rail contact with different friction coefficient were analyzed.Attack Angle is 0 mard,friction coefficient values were taken respectively as 0.1,0.3 and 0.5.

Figure 4 Distribution of Mises stress without transverse quantity

Figure 5 Distribution of Mises stress with 5mm transverse quantity
Table 6 Results of ABAQUS with different friction coefficient

It is not hard to see from Table 5,the friction coefficient has a great influence on tangential characteristics of wheel/rail rolling contact.With the increase of friction coefficient,the maximum transverse shear stress and the maximum longitudinal shear stress increase concurrently.And it has no obvious influence on the normal characteristics and the size of the contact spot.
4 Conclusions
Under the combination of UM multi-body dynamics simulation software and ABAQUS finite element software,characteristics of wheel/rail rolling contact are analyzed contrastively.This article provides a three-dimensional display of related results.The main following conclusions were obtained:
(1)The results of simulation obtained by finite element method and the results obtained by multi-body dynamics simulation is similar.They are all valid.But the results obtained by finite element method based on the theory of elastic-plastic is more visualized and closer to real.
(2)Mises stress,the normal contact stress,the transverse shear stress and the longitudinal shear stress have the maximum value in the absence of transverse quantity.
(3)The maximum Mises stress appears on the rail contact surface.With the increase of wheel/rail transverse quantity,the maximum Mises reduces and the distribution area of Mises stress also tends to be reduced.
(4)The friction coefficient has a great influence on tangential characteristics of wheel/rail rolling contact.The shear stress on rail surface increases with the increase of friction coefficient.The rationality of the value of friction coefficient will directly affect the life of wheel/rail.
Acknowledgement
The authors wish to acknowledge the support and motivation provided by the national natural science fund project(No.11302137).
References
[1]Guo J.,2006.Study of the Mechanism of Wheel/Rail Rolling Contact Fatigue Damage[J].Journal of Southwest Jiaotong University,11(12):15-19.
[2]Gladwell G.M.l.,1991.Contact Problem in the Classic Theory of Elastic(Ed)[M].Beijing:Beijing Institute of Technology Press.
[3]Zhong W.,2012.The Comparative Study on the Fatigue Wear of High-speed and Heavy Rail[J].Tribology,1(3):15-18.
[4]Li Z.J.,2012.Analysis of Abrasion and Stripping Problem under the Condition of the Curve Overloading Rail[J].Railway Technical Supervision,10(6):20-23.
[5]Liu Y.C.,2014.Shape and the Tangential Force Characteristic of Wheel/Rail Contact Relationship[J].Foreign Railway Vehicle,6(11):40-43.
[6]Braghin F,Lewis R,Dwyer-Joyce R S,et al.,2014.A Mathematical Model to Predict Railway Wheel Profile Evolution Due to Wear[J].Wear,261(12):1253-1264.
[7]Chen H.C.,1997.The Research of High-speed Wheel/Rail Rolling Contact Problem[J].Railway Science Research Institute,4(11):25-30.
ICRE2016-International Conference on Railway Engineering