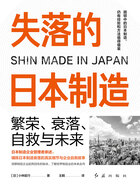
30年来,转移到海外的日本品牌的生产情况
泡沫经济崩溃后,日本的服装产业和家电产业相继出走到制造成本相对低廉的国家,因为在那里,这些产业能够以更低廉的原材料、劳动力成本制造出产品。当时奔赴国外的从事制造、采购相关工作的负责人,以及做出如此决策的经营者恐怕都是这么想的:“之前长年采用日本中小下包公司供应零部件的方法,是多么浪费啊!”
这种“不劳而获”的状态带给品牌厂商们一种在未开拓的年代随手挖出大量金银财宝的淘金者一般的心情。
出海的各个品牌厂商雇佣廉价劳动力,建起本公司的生产线,恐怕是想要将以往派单给下包公司的零部件尽量都转为本公司制造。
他们心里恐怕是这么盘算的:零部件全都由本公司制造,一定可以生产出质量和品质和以往一样的产品吧。
然而,那就是“Made in Japan”衰败的开始。
日本享誉世界的制造精神就是从那时开始崩溃的。
聊聊我所知道的事实吧。
之前一直将线圈制造派单给我们的品牌厂商,在业务转移到马来西亚的柔佛州之后,购入了数台和我们公司里一样的全自动绕线机。
后来我偶然得到了一个去拜访那边工厂的机会,发现被称为“喷嘴”的一种制造线圈所需的引导零部件在那家工厂频繁地发生扭曲变形的情况,每个月都要更换几十根。
“喷嘴”是为了将线圈均匀缠绕所需的最重要的零件。
通常,这种自动绕线机可以一次性绕好12个线圈,但要将12个喷嘴一丝不差地设置在线圈卷轴的上方,设置位置的精度决定了线圈绕线的精度,即决定了线圈能否一丝不乱地均匀缠绕。
我们公司也使用这种12轴的绕线机来生产线圈,喷嘴的位置设置得稍有差错就会打破线圈的平衡,从而无法生产出符合尺寸、特性要求的产品。
当时,这种喷嘴的成本为每根8000日元左右,为了制造单品加工费不过4~5日元的产品,1个月只要损坏1~2根这样的喷嘴,就会入不敷出了。
若是每个月有几十根喷嘴扭曲变形,是不可能造出能媲美我们公司产品品质的线圈的。PPM管理(即100万个产品之中,不合格品不超过1个的品质目标)更是想都别想。
如果像这样与以前的品质截然不同的零件能通过品牌厂商的质检流程,像以前一样在市场上流通的话,那这种产品与之前的品质差异可谓一目了然,恐怕也不能称之为“Made in Japan”或“日本品质”了。
还有一个事例,有家在泰国拥有工厂的品牌厂商向我们下了相机零部件相关的订单,按照要求,要设计一种线圈,让它完成这个部件中原本由两个线圈完成的工作。这可是跨时代的装置,所以我们满怀期待地在本公司的海外工厂立了项。
这个产品的线圈需要使用直径0.03毫米的极细线来制造,如果处理不小心,电线很容易被折断。
虽然线圈本身是由海外工厂直接发送到泰国,但可能是由于组装方法不得当,每个月都会产生百分之几十的不合格品。
如果生产过程中出现不合格品,那终端用户手中必然也会出现一定量的不合格品。
如果快要断掉的线圈也能通过检查顺利出货,那客户投诉想必会源源不断吧。
对于我们公司来说,对方购买的线圈数量多于最初的计划,提升了我们的销售额,自然应该感到开心。可是,我们提供的品质完好的线圈被大量浪费终究不是一件好事。
“需要我们帮忙吗?”曾经,我们也向这个项目的日本采购负责人表达了想要帮忙改善品质的意愿,但泰国是泰国,日本是日本,似乎日本方面也很难插手泰国厂商的事情。后来,这个项目由于产品不合格率偏高而陷入困境,不过两年左右就失败了。
我还曾造访过另一家日本著名家电品牌的泰国工厂,当时可真是让我感到震惊。
那是一道需要3名工人共同作业的工序,但当时我就意识到,只要做一些简单的夹具,这道工序完全可以由1名工人来完成。
可是当时似乎完全没人在工作合理化、效率化方面进行改良。
除此以外,品牌厂商在出海制造时还会发生下面这样的事。
我们公司曾经设计制造了一批夹具分发给临时工,让他们在公司内部用自动机组合加工。当时的发包企业可能觉得这个方法挺好,就把这种夹具和制造方案一起带到了海外。我们公司也觉得这项业务还是当地处理比较好,就把制造方法和相关技巧都带过去了。
然而,那家海外工厂真能做出符合公司品质要求的产品吗?
我认为,日本产品制造的技巧毫无疑问掌握在我们中小微企业手中。
但是,就算中小微企业把各种制造技巧都带往国外,产生技巧的思想、精确扎实的制造本质却难以被模仿。这一点,希望大家能够明白。